Swiss watchmaking industry embraces the circular economy

Powering through some 120,000 tonnes of stainless steel per year, Switzerland’s industry is one of Europe’s hungriest consumers of the metal. As the industry comes under increased pressure to reduce its environmental impact, local entrepreneurs are moving to establish recycling chains to enable this valuable raw material to be reused including in the watchmaking industry.
At first glance, Precycling, a recycling centre in Reconvilier in Canton Bern, looks like many others in Switzerland. In the courtyard, the shell of an old car held aloft by a crane is about to experience the end of its days. Close by, dozens of square cubic metres of wood, paper, cardboard, empty bottles, rags, and other materials are waiting to be distributed to specialized recycling channels.

Adjoining this carefully sorted hodgepodge of unwanted stuff is an imposing office building. With its heavy security and large bay windows, the conference room features designer chairs and a large flat screen TV; a striking contrast to the image normally associated with a recycling depot.
“We have had to adapt our standards to those of the watchmaking sector,” explains Precycling director Alexandre Haussener.

Aside from its traditional recycling activities, the Bernese business disassembles hundreds of thousands of watch components – in the strictest of secrecy, of course – collected from some 20 brands in the region. Mostly they are unsold watches that have been taken off the market in order not to feed the grey market, but there are also faulty factory pieces in the mix as well.

Jura gold
Until recently, Switzerland’s watchmaking industry had largely escaped the ire of climate change and sustainability. Watches taken out of the market were simply destroyed. Things are changing. A 2018 report by the World Wildlife Fund (WWF) described the social and environmental impacts of the watchmaking sector as “much more significant than one would have thought at first glance”.
The WWF said the sector’s demand for large quantities of precious raw materials, coupled with the lack of transparency around watchmaking, was “extremely worrying”.
“Until a few years ago, excess watchmaking stocks were often crushed using steamrollers. Sorting was very basic,” explains Precycling technical manager Gilles Fischer.

In Reconvilier, the different metals — gold, silver, titanium, steel, etc. — are now carefully separated, often by hand, before being shredded and reused by different industries : mostly watchmaking, medical supplies and manufacturing. One of the most precious metals recovered from the watches is steel. It is often referred to as the “black gold” of the Jura due to its dark colour.
The steel recovered at Reconvilier — more than 20 tonnes per month — is transported to the ovens at a factory in the French region of Savoie, where it is melted down and transformed into machinable steel bars before it is reused by Swiss industry.
One word: regionalization
“Steel is the most used raw material in watchmaking. This part of the watchmaking industry alone consumes nearly 9,000 tonnes a year. But the nearly 1,500 tonnes of steel shavings produced by machining watch parts are usually sent to China to be melted down and recycled into bars of mediocre quality. It’s an ecological and economic aberration,” comments Raphaël Broye, founder of Panatere, Switzerland’s first recycled stainless-steel business.
Broye aims to keep the steel in Switzerland. His next plan is to build a CHF10m mobile, solar-powered industrial oven that, in theory, will make it possible to endlessly use recycled steel that has not once left Switzerland.
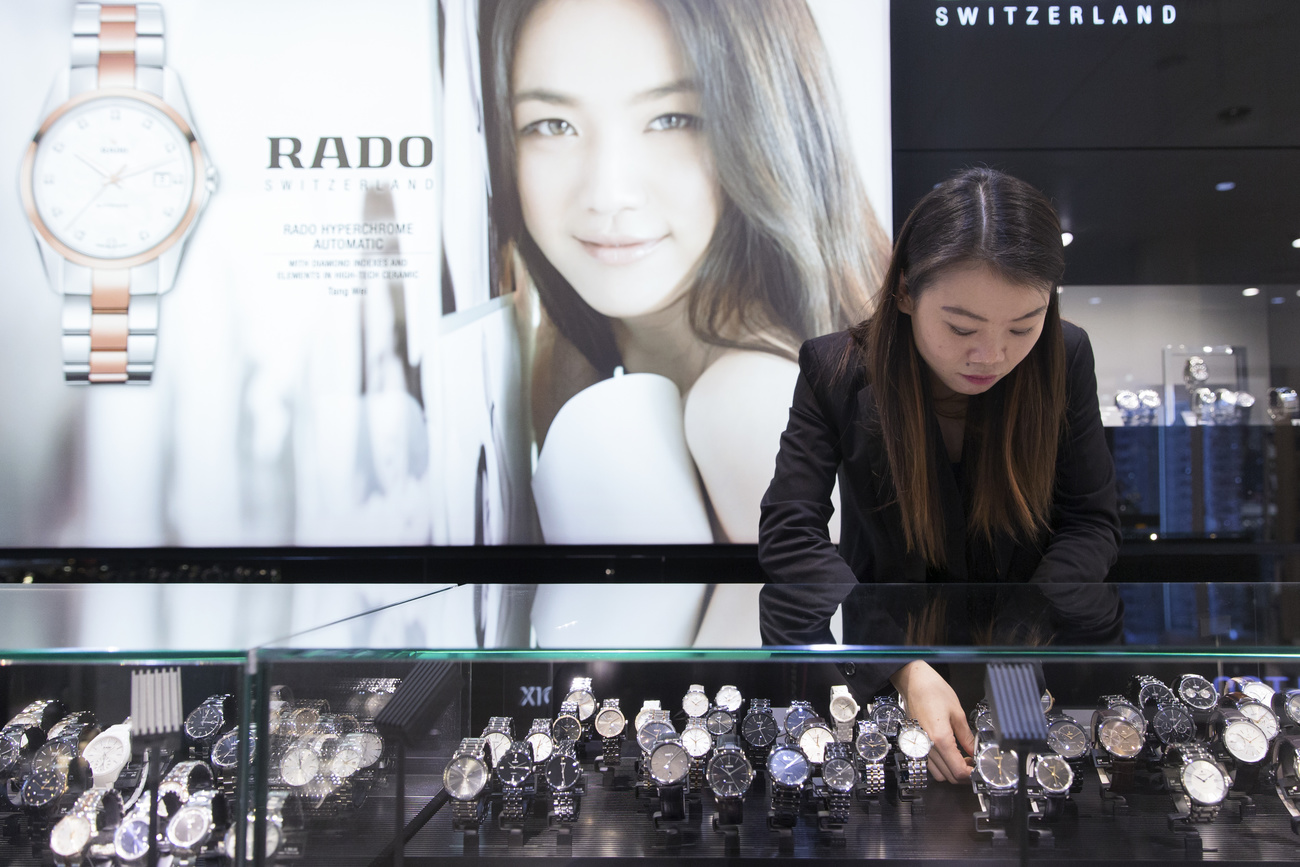
More
Five steps to keep the Swiss watchmaking industry ticking
“We are in contact with the big watchmaking companies, who are interested in our recycled steel. Over the coming decades, more local production is set to be a key focus for the Swiss watchmaking industry,” comments Broye.

100% recycled steel watch
Start-up ID Genève Watches recently launched the first watch made from Swiss recycled steel. During a crowdfunding campaign in December 2020, 300 pieces of the model dubbed ‘Circular1’ sold out in less than 48 hours. Priced at CHF3,500 and labelled ‘Circular Swiss Made’, the timepieces included a recycled case, a reconditioned automatic movement, and a band made from the residue of grapes after vinification.
“We have had excellent feedback from our customers. For the most part, they are ‘millennials’ who want to flaunt their activism on their wrists, and not just wear an ostentatious symbol of wealth,” says ID Genève Watches co-founder Nicolas Freudiger.

Today, a large section of the Swiss industry’s traditional clientele, especially in Asian countries, remain resistant to the idea of wearing a prestigious timepiece made from recycled materials, admits Freudiger. However, several studies show that even in the luxury segment, sustainability is becoming a more important factor. A report published by Deloitte in June 2021 shows that 50 % of consumers are now taking sustainability into account before purchasing a watch.
In Reconvilier, Haussener is confident the winds of the industry are changing and believes his business has a strong future.
“We are moving towards a much more sustainable and ecological watchmaking industry. I am convinced that recycled steel will become standard for most Swiss watchmakers within a few years,” he says.
Translated from French by Sophie Douez; edited by Virginie Mangin
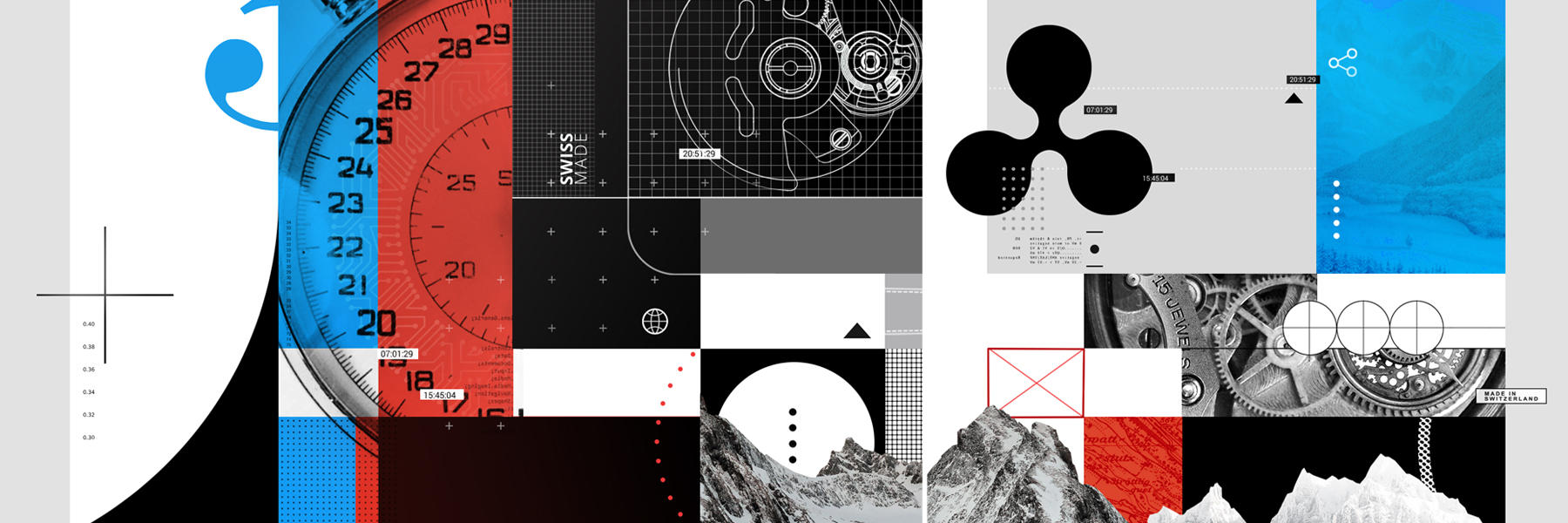
More
Can Swiss watchmakers survive another century of disruption?
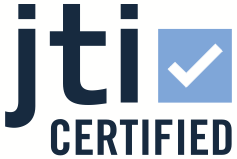
In compliance with the JTI standards
More: SWI swissinfo.ch certified by the Journalism Trust Initiative
You can find an overview of ongoing debates with our journalists here . Please join us!
If you want to start a conversation about a topic raised in this article or want to report factual errors, email us at english@swissinfo.ch.