Next-gen batteries: Swiss researchers help lead the charge
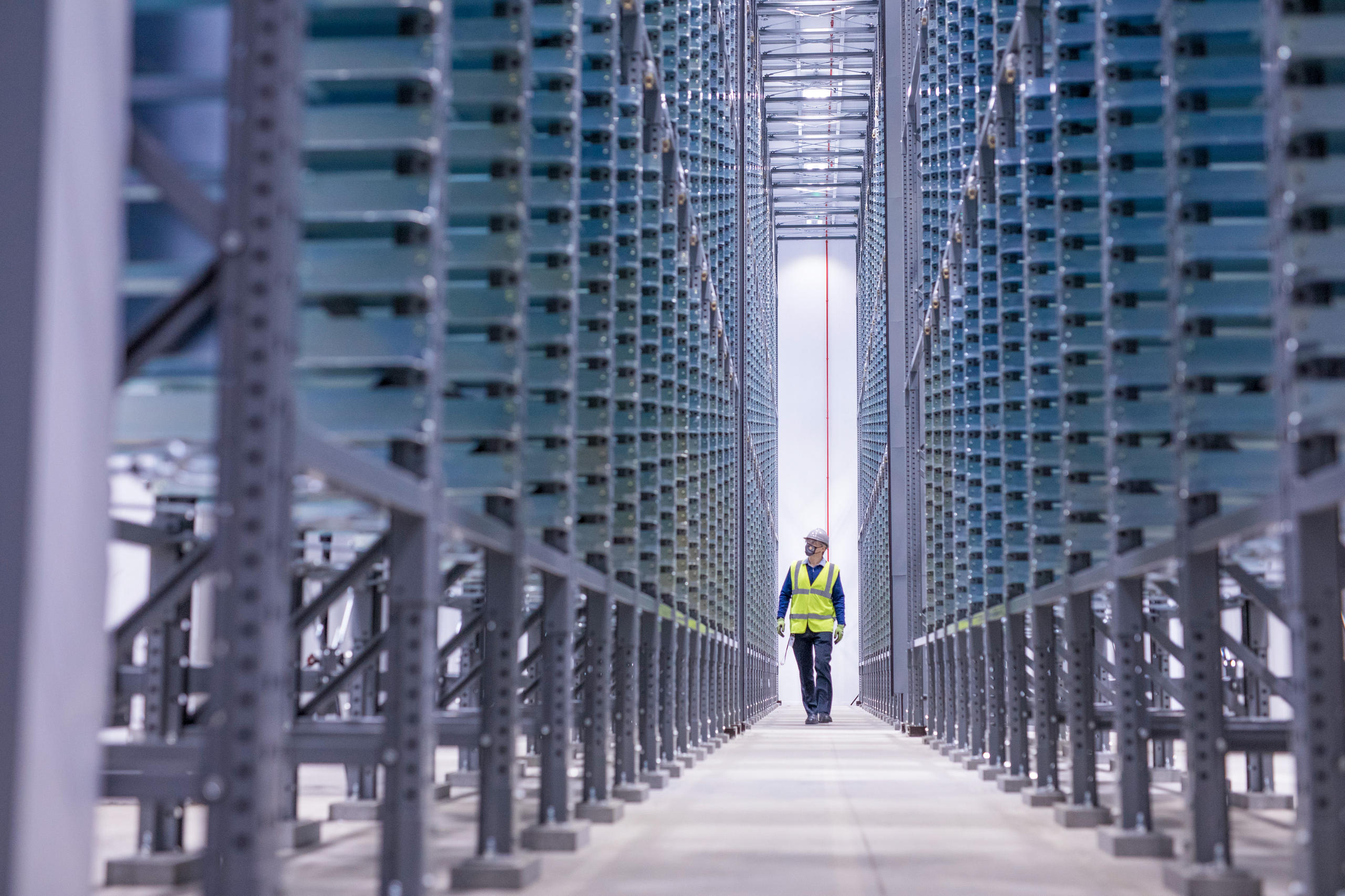
Batteries are everywhere – in our phones, laptops and cars – but the ideal low-cost, high-performance technologies of the future have so far eluded scientists. Major European and Swiss research initiatives are trying to meet demand for battery innovation and energy storage, with results expected in the coming decade.
“Batteries could enable 30% of the required reductions in carbon emissions in the transport and power sectors, provide access to electricity to 600 million people who currently have no access, and create 10 million safe and sustainable jobs around the world,” the Geneva-based World Economic Forum recently declared in a key report.
Asia dominates the mainstream battery market, with over 90% of production taking place in China, Korea and Japan. But Europe wants to catch up fast. Driven by its car industry, the European Union wants to establish battery cell manufacturing on the continent and prevent technological dependence on other parts of the world.

“At the moment we are fast-followers, but the EU’s idea is that we have a good base in terms of battery research and innovation,” explains Corsin Battaglia, an expert at the Swiss Federal Laboratories for Materials Science and Technology (Empa). Non-EU-member Switzerland is closely involved in European battery research projects.
Four years ago, Brussels launched the European Battery Alliance to build up production and R&D capacities. As part of this development, almost 40 mega-battery plants, so-called giga-factories, are planned across Europe, according to the Transport & Environment NGO. If they all become operational, the continent could win a 20% share of the global battery market by 2025 – annually worth €250 billion (CHF270 billion).
One of the first fully European giga-factories is Northvolt Ett, being built in northern Sweden. Northvolt says it will be able to produce enough batteries for one million electric vehicles a year.
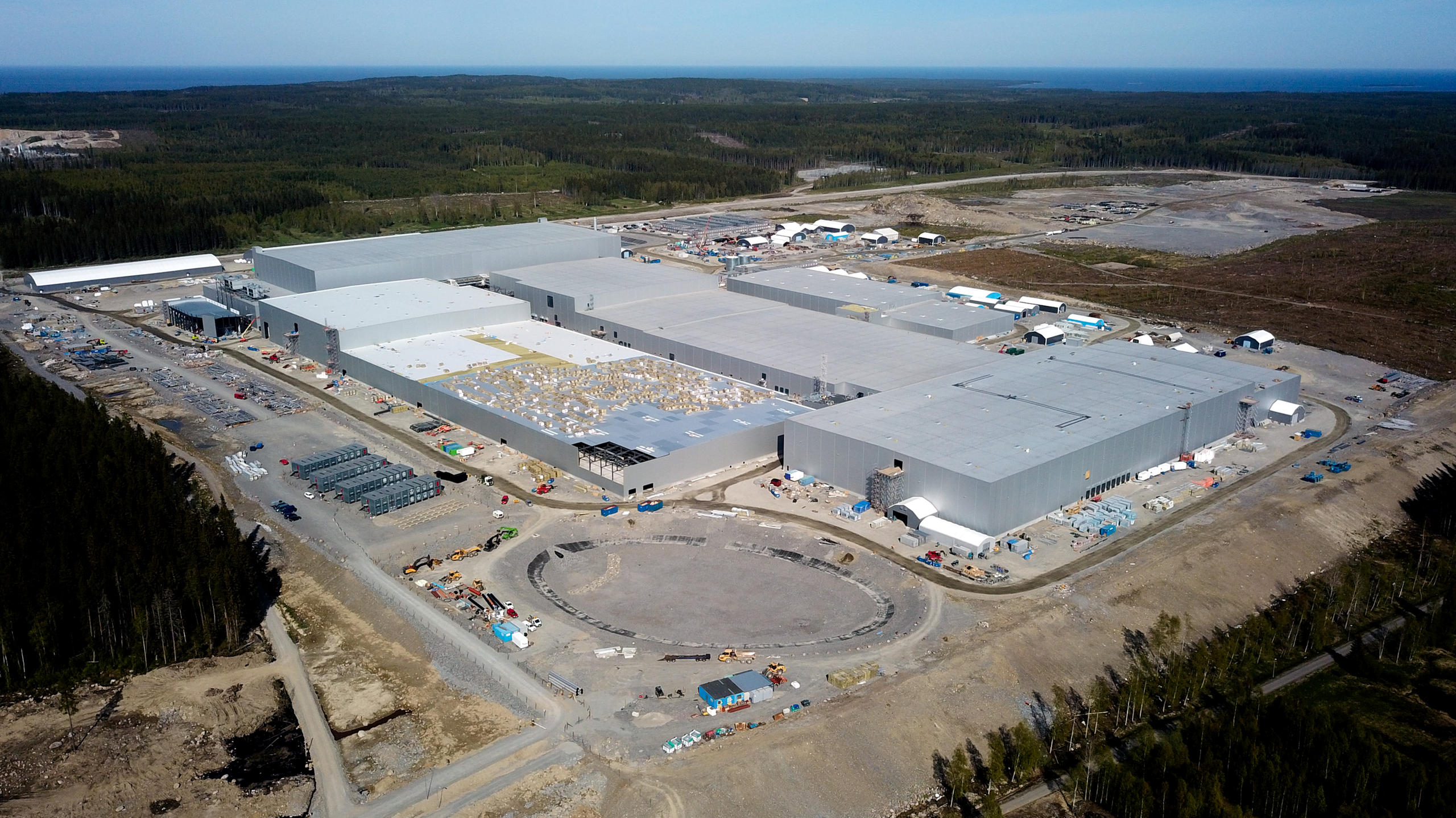
No giga-factories are currently planned in Switzerland, but the Alpine country is closely linked to industry developments via its research institutes and specialist firms.
“Whether it’s materials, cell and pack integration, electronics, battery management systems, recycling and mobility or stationary storage, there are lots of companies in Switzerland that are active in the batteries field or even world leaders,” says Battaglia.
Self-healing batteries
Lithium-ion batteries have been the dominant storage technology for years, with demand expected to multiply ten-fold over the next decade. Over the past 30 years the price has dropped by almost 100% but the science has remained largely unchanged. Alternative battery technologies, such as longer-lasting components that store more energy, will be needed to meet future demand.
This is where the €40-million European Battery 2030+ research initiative comes in. Launched last year, the scheme comprises seven large research projects supported by nine European countries, including Switzerland. One those projects is “HIDDEN”, aimed at improving the average lithium-ion battery’s lifespan and energy density by 50%.
The growth of tiny fibre-like formations inside batteries, known as dendrites, is a real problem for the longevity of lithium metal batteries, explains Axel Fuerst, a HIDDEN project manager at the Bern University of Applied Sciences.
“Lithium metal has a very high energy density and can therefore be used to make lighter, more efficient batteries. But the dendrites grow very fast, and the lifespan is short for such cells,” he says.
To solve the problem, the team is working on a self-healing process inside the battery. They hope that specially developed thermotropic ionic liquid crystal electrolytes, together with additives and a piezoelectric separator that creates an electric field, can together break up and suppress the growth of dendrites. The team is building a first concept model that will be validated by 2023 and later scaled up.
Using fewer rare metals
Meanwhile, Battaglia and his Empa team are coordinating “SENSE”, a European lithium-ion battery research project that is looking to produce a so-called “generation 3b” lithium-ion battery with a silicon-graphite composite anode and a nickel-rich Nickel Manganese Cobalt (NMC) cathode. The aim is to improve energy density, allowing an extended driving range for vehicles, boost fast-charging and use fewer rare metals.

“We want to reduce the amount of cobalt and increase the amount of nickel,” says the Empa researcher.
Cobalt is the one of the most expensive materials in a battery. Producers are trying to reduce its use as sourcing it can be a challenge. Around 70% of the world’s cobalt comes from the Democratic Republic of Congo, where conditions for miners are problematic, and most refining operations for cobalt are situated in China.
Creating the ideal battery is complicated and often a trade-off, explains Battaglia. Nickel increases the battery’s energy density and is cheaper, but it makes the battery degrade faster, he explains.
The scientists are experimenting with adding silicon to the graphite anode. Silicon is an interesting material for battery researchers as it can store around 10 times the energy of graphite. But during battery cycling, silicon tends to expand and then fall apart, leading to fast performance loss.
The team is also working on developing new fast-charging sensors so that batteries can be charged more quickly and efficiently.
“We want to understand the local temperature and potential inside the battery and to measure inside the cell [more quickly] so we can push fast charging,” says Battaglia.

Solid-state batteries
There is much excitement in the battery world around solid-state batteries, which use solid electrolytes to replace the flammable liquid solution in lithium-ion batteries. These are said to be more efficient, safer and use fewer raw materials. Prototypes suggest that they could store up to 80% more energy than lithium-ion units of the same weight and volume.
Battaglia says such technologies appear to offer many benefits, but for now they remain “potential” advantages that are limited to the lab. It’s difficult to develop a battery with high storage capacity that also has a long lifetime, he says.
“It’s not a problem to make a battery with double the energy density but perhaps I can only charge it 20 times and then it’s dead,” the researcher explains. Whereas the battery’s energy density can be doubled by replacing graphite with lithium metal, charging a lithium-heavy battery too quickly results in dendrites that reduce its lifespan.
If they go mainstream, solid-state lithium batteries could solve both the energy density and longevity problems. Empa is working with a dozen European partners on the “SOLIDIFY” project, which aims to develop manufacturing processes for so-called “generation 4b” batteries, solid-state batteries that could be ready to market in ten years.

Efficient stationary storage
Stationary systems that can stockpile renewable energy are also set for massive expansion in the coming decades. Lithium-ion and lithium nickel manganese cobalt oxide (NMC) batteries are already being used to store solar and wind energy produced in homes. Scientists are now exploring alternatives that use zinc, vanadium or sodium, for example, which are proving to be well-suited for stationary storage. But they need to be scaled up to meet rising demand and to become cost competitive.
The conferenceExternal link in Winterthur, Switzerland on September 2-3, brings together participants from the public and private sectors to discuss challenges and solutions to achieving the Sustainable Development Goals as set out by the United Nations. Renewable energy and the sourcing of raw materials is one of the key themes of the 2021 event.
SWI swissinfo.ch, as media partner, is co-organising and moderating a forum at this year’s symposium on effective and sustainable communication, which will include a presentation on “solutions journalism”. Follow along and find more information here.External link
Empa is one of twelve partners involved in trying to make that happen through the European SOLSTICE battery project that also involves Swiss firms FZSONICK and Quantis. Their aim is to develop sodium-zinc molten salt batteries operating at high temperatures that can be used to store energy.
“The most important advantage is the replacement of nickel in the cathode with cheap and abundant zinc to obtain a sustainable storage system at lower cost and minimal environmental impact,” explains Andrea Pozzi, FZSOnick’s innovation and development manager.
With batteries set to grow in importance in the coming decades as the number of renewable energy storage systems and electric vehicles multiply, Swiss firms – and not just existing players – are looking to profit, says Battaglia.
“I get approached a lot by Swiss companies that are not in the battery field but they see this as a market that they can enter with their manufacturing or integration expertise.”
Another major energy storage project underway in Switzerland is a collaboration between the Valais-based chemical firm Lonza and US company Natron Energy. In April 2021, they announced a strategic agreement for the supply of Prussian Blue powder for sodium-ion batteries.
Lonza Specialty Ingredients will produce Prussian Blue for Natron at its Visp facility. From the end of next year, the materials will be used to manufacture battery electrodes at a new facility planned for 100 staff near Sion. Swiss-manufactured electrodes will then be transported to the US to be integrated into Natron’s energy storage products.
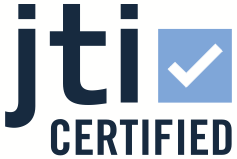
In compliance with the JTI standards
More: SWI swissinfo.ch certified by the Journalism Trust Initiative
You can find an overview of ongoing debates with our journalists here . Please join us!
If you want to start a conversation about a topic raised in this article or want to report factual errors, email us at english@swissinfo.ch.