
Solar Impulse makes a material difference

While the Solar Impulse team has begun a series of landmark test flights across the United States, work is under way in Switzerland on cutting-edge materials for the next version of the solar-powered aircraft.
The goal of the creators of Solar Impulse – Bertrand Piccard and André Borschberg – is not just to set records but to promote the implementation of renewable energy technologies. With some 80 partners, including many Swiss companies, who have helped conceive, build, test and fly the prototype, the wealth of research generated by the project has stretched far beyond this initial aspiration.
Back home in western Switzerland, away from the cheers and cameras, construction of the next Solar Impulse aircraft, HB-SIB, is under way. To the Solar Impulse industry partners and its scientific advisor, the Swiss Federal Institute of Technology in Lausanne (EPFL), the solar-powered plane is a concentration of technological challenges – not least of which has been finding the right materials.
There is not a single rivet in the Solar Impulse; all its parts are glued together. Looking for an ultra-light but durable material for their dream plane, the Solar Impulse engineers had to push the boundaries of composite material development.
The challenge was taken up by Décision SA and North TPT, two companies in the Lausanne region working in close collaboration with EPFL. Interestingly both companies have a nautical background.
The 2013 Across America flights kicked off on May 3. It has a five-stop itinerary: from San Francisco (California) to Phoenix (Arizona), to Dallas (Texas) to Saint Louis (Missouri) or Atlanta (Georgia), ending in Washington D.C. and New York City.
The first Solar Impulse aircraft HB-SIA was unveiled on June 26, 2009. The first test flights began the following year, culminating in the first night flight in solar aviation history on July 7 2010, lasting more than 26 hours.
In September 2010, Solar Impulse flew across Switzerland landing in Geneva and Zurich airports. 2011 saw the first flight outside Switzerland, first to Brussels and then on to Paris.
In seven legs, Solar Impulse flew from Payerne, Switzerland to Rabat, Morocco and back in 2012. This year construction of the next Solar Impulse plane HB-SIB is taking place. The ultimate goal is a round-the-world flight in 2015.
Ultra-light
The ultra-light skeleton-frame fuselage, cabin and wings of the first prototype, HB-SIA, now flying in the United States, were made by Décision in collaboration with EPFL. It took the company a year of tests and collaboration to eventually come up with the right honeycomb carbon-fibre sandwich design for the first plane using carbon sheets weighing just 93 grams per square metre.
“It’s high tech but at the same time very artisanal,” Décision director, Bertrand Cardis explained, walking around the workshops which have produced several Alinghi yachts and a wing for Yves Rossy (aka Jetman).
Technicians are currently preparing individual panels for the new Solar Impulse fuselage and working on assembling it. “You’re talking up to 6,000 work hours per piece,” Cardis said.
The aim is to have an even lighter plane next time with a wider wing span of 72 metres and more room for solar panels. The carbon sheets being used for the new aircraft are three times lighter than paper, down to just 25 grams per square metre.
“For the development of extreme projects you have to leave your comfort zone,” Cardis pointed out. “You enter a zone where you take risks and then have to minimise those risks. This has involved lots of research with the EPFL.”
The geographical closeness of the main players in materials research and development for this project is a big advantage, according to Pascal Vuilliomenet of EPFL. “What we have here is a cluster of expertise which is invaluable,” he told swissinfo.ch
More layers
Décision’s supplier, North TPT, is only a few minutes’ drive away. Based in a converted cable factory, North TPT developed new sail material for Alinghi ahead of the 2007 Americas Cup. The material was created in a mould from a patchwork of pieces made from a revolutionary new type of carbon composite, which is mainly used for cars, boats and trains.
Carbon composite consists of layers of ‘prepreg’ fibre sheet (a mix of reinforced fibre and resin), which are baked to set. North TPT, working with EPFL researchers, is developing a much thinner ply material. This material is composed of many more layers of fibre, laid over each other in different directions, lighter and stronger than what has come before.
“In effect it’s like having more pixels in a photograph,” said North TPT managing director François Mordasini.
The new material is so thin that it needs a special computer-operated robot to place the different layers of fibre at different angles, producing custom-made sheets or blocks of carbon composite, which can be used to make anything from fishing rods to watch parts to Formula One gear boxes.
North TPT also had to develop new computer programmes to use for the calculation of the composite structure, adapted to handle more numerous layers. With these elements in place, the new material can be fully exploited.
“We have put together a new tool box that allows us to optimise the materials on an individual basis,” Mordasini added.
Put to the test
The thin-ply composite has different properties to standard composite and these are being tested by Robin Amacher and colleagues at the Laboratory of Applied Mechanics and Reliability Analysis at EPFL.
“What’s remarkable about this composite is that it has a much higher breaking point and the break is cleaner. Resistance to fatigue [wear and tear] also gives astonishing results. This allows the designer to make full use of the material’s performance,” Amacher told swissinfo.ch.
“We are not just measuring values but we are also learning how materials break. Once you know that you can make proposals for improvement,” he added.
EPFL joined the Solar Impulse project in 2003, when it carried out a feasibility study. Since then a series of research axes were set up, including human-machine interface sensors – Solar Impulse pilots have to stay alert for long stretches. More work will be done in this area during the planned simulator tests for the new plane in December.
“Discovery projects such as Solar Impulse are worthwhile for us not just for showcasing technology but because our students are involved in high quality innovative research where they see their contribution used immediately. This kind of technology transfer benefits everyone,” Vuilliomenet said.
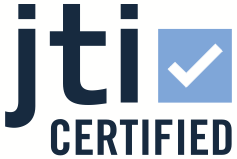
In compliance with the JTI standards
More: SWI swissinfo.ch certified by the Journalism Trust Initiative
You can find an overview of ongoing debates with our journalists here . Please join us!
If you want to start a conversation about a topic raised in this article or want to report factual errors, email us at english@swissinfo.ch.